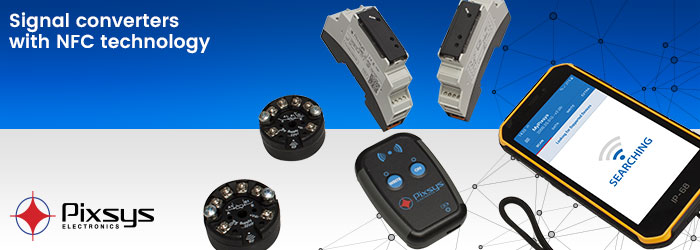
Over 100.000!
Outstanding result for the signal converters with NFC technology
Only a few years ago Pixsys launched on the market the innovative signal converters with NFC-Technology. We were front-runners and among the first to believe in the potential of this programming mode: we won the bet, as confirmed by over 100.000 installations on machines and plants of our customers.
Play in advance.
For those working in the field of technological innovation, it is often crucial to know how to seize the moment and anticipate. So it was also for the NFC technology applied to signal converters: when this new perspective appeared on the market, Pixsys immediately realized its potential. Indeed, in a short time this range of products proved to be very effective and, and for this reason it is increasingly widespread.
Would you like to test by yourself? Request a demo sample!
You can experience this unique programming mode and test the performances of Pixsys converters in your application and with your sensors. Click on the link below and fill in the form to get your free sample.
Main features at a glance.
Why is the NFC product family so popular with our customers? Here are the key features of these devices:
- Each product code is programmable for different types of sensors
- Process variable can be monitored and historical trend can be visualized by App MyPixsys
- Reliable and robust electronics
- Available with same features both for DIN-B head-mounting or DIN-rail mounting (DIN43880)
Additional new versions coming soon.
The range is constantly expanding. Beside series with Atex approval for hazardous areas/ explosive atmospheres, we are adding model with HART protocol and the next step will be the IO-Link model, awaiting further future developments.
Case History: Boom of colored pencils during lockdown.
The pandemic has overwhelmed and upset every aspect of our lives, including the relationship between supply and demand for the most diverse types of products on the market. Thus, if for many companies there has been a sharp decline in activity and sales, others have found themselves having to satisfy a sudden increase of demand. A concrete example: the large number of children forced to home-schooling needed a considerable amount of colored pencils to draw and paint.
This is why the well-known Swedish multinational that supplies products for home and for children has requested an immediate and huge increase in production from its suppliers .And Its main supplier of pastels relied on different Pixsys products to respond effectively to this increased demand. Our controls, interfaces, actuators and sensors have supported the different changes that had to be made in real time to manufacturing processes to face the increased demand: a new network of substations for mixing and weighing colors at a controlled temperature; the integration with the transport system towards the controlled heating molding machines to avoid lumps during mixing; color labeling and packaging systems; the integration of data into the company MES to simplify predictive maintenance and obtain all the production and quality statistics required by customer.
Our products have therefore allowed a company to be performing successfully under critical circumstances and for many children not to be without their pencils during the long days spent at home: we are proud of our contribution!
Feedback analysis, milestone of constant improvement.
Ideally each product placed on the market should be free from defects and anomalies. However we all know that it is technically and physiologically impossible for 100% of production to be immune to any problem during its life cycle.
This is why technical post-sales service becomes crucial not only to support customers but also for our own manufacturing. Failure analysis is essential for future improvement. Understanding root causes over the time has led to significant adding of software parameters, improve design of both hardware and software.
Effective yet simple: a functional protocol.
How does it work concretely? We developed a detailed protocol to trace and analyze the feedbacks we regularly get from our customers that improve, correct and implement the performance of products, in a spiralizing evolution process that accredits them on the market as increasingly mature and reliable devices.
To communicate with us, we provide customers with multiple channels: from phone calls to direct messaging, through online assistance Forum that makes a first level of analysis of installation, configuration and performance problems available and immediately accessible to each of our customers.
All of our most recent products are also designed for sending parametric configurations or for updating software versions in on-site mode which involves the use of common messaging applications combined with companion App My Pixsys or via Transfer File applications, allowing the customer to independently solve many cases.
When is it necessary to activate the RMA procedure for returning hardware to the manufacturer, just access “My device” section on the pixsys.net website to independently activate RMA process. This is the beginning of analysis process, which we carry out with extreme accuracy in the shortest possible time.